Introduction
This article offers a comprehensive summary of the different simulations and work undertaken by the formula student team EETAC FS Team, using ANSYS software.
Through this summary, we will delve into the key projects undertaken by the EETAC FS Team and explore the ways in which ANSYS software has played an important role in their car design.
Objectives
The objectives of the team, regarding Ansys, for the 2022-2023 season are to have a first contact and increase understanding of the fluid simulation tools (CFX and Fluent) in the early phases of development, and advance to deeper understanding and first simulation results of our SolidWorks 3D models in order to analyse the aerodynamic performance of our car.
Details
In this year we have spent most of our time learning how to use the powerful Ansys software in other to create the aerodynamic parts of the single-seat vehicle.
Talking a bit about the work done especially this first part of the year 2023, simulations of the nosecone, the bodywork, the diffuser, and all parts together have been done.
Nevertheless, we are really in a learning and comprehension phase regarding Ansys and we continue every week pushing our acknowledge boundaries in order to get better and better simulations every time.
We first always model the piece in 3D software, after that we create the fluid domine, define boundary conditions, create a mesh and simulate with Fluent or CFX solver. In these simulations CFX solver have been used in order to perform the simulations.
Nosecone
In order to follow our development path, we have simulated 2 different models for the nosecone.
In the first model, we pretend to measure the downforce done by a typical FSAE nosecone, while in second one we pretend to improve the previous model and reduce drag with a less pronounced drop and more rounded edges.
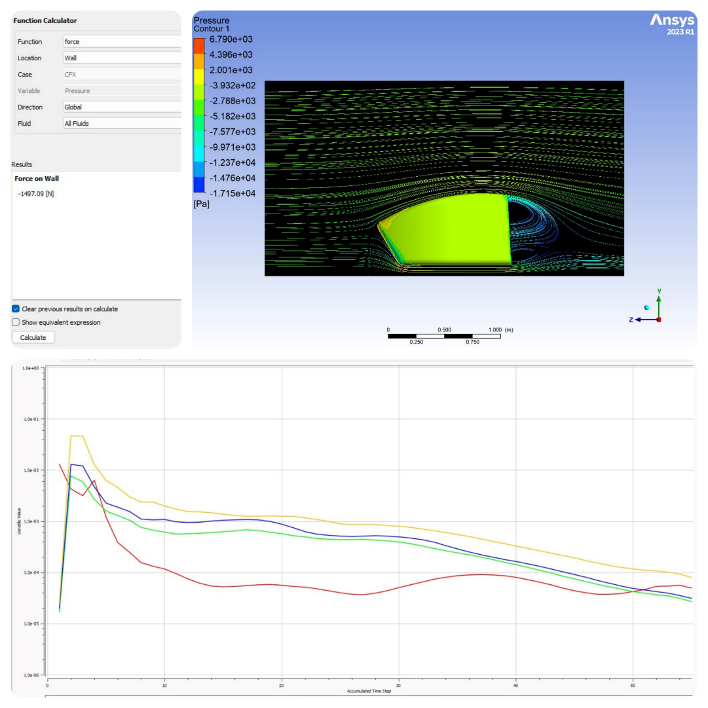
Figure 1: Simulated force, pressure contour, and parameters by iteration in the nosecone (Model 1)
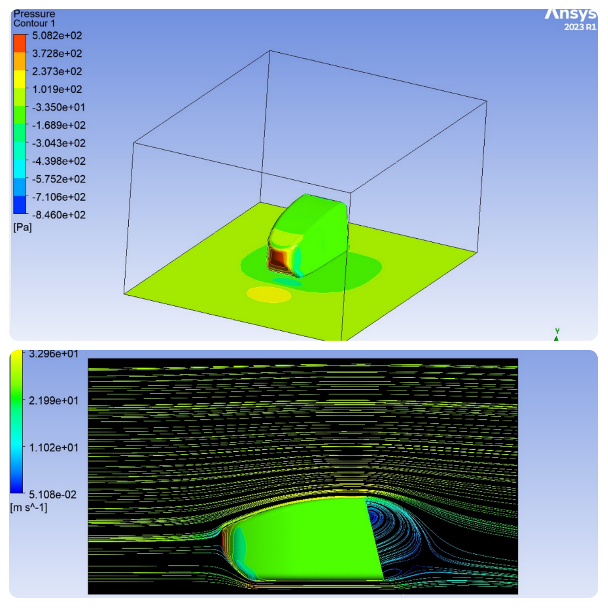
Figure 2: Simulated pressure contour and velocity streamlines on the nosecone (Model 2)
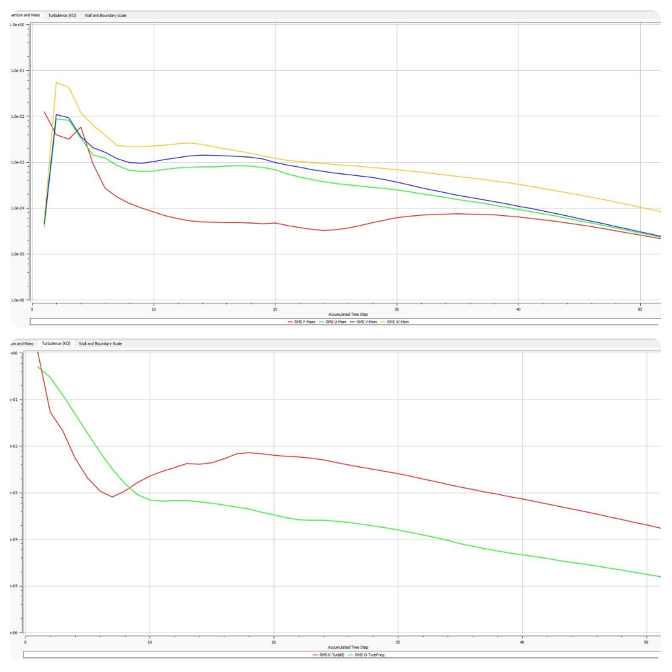
Figure 3: Graphics of simulation parameters and turbulence by iterations in nosecone (Model 2)
Diffuser
The diffuser is an essential part in a competition car, because is the part that generates most of the downforce. Because of this fact, we had designed more than three different models of diffuser and after all, this model is the final one, with a simple and straight air inlet and a not very pronounced outlet and some vertical plates that laminate the flow to avoid the separation of the boundary layer.
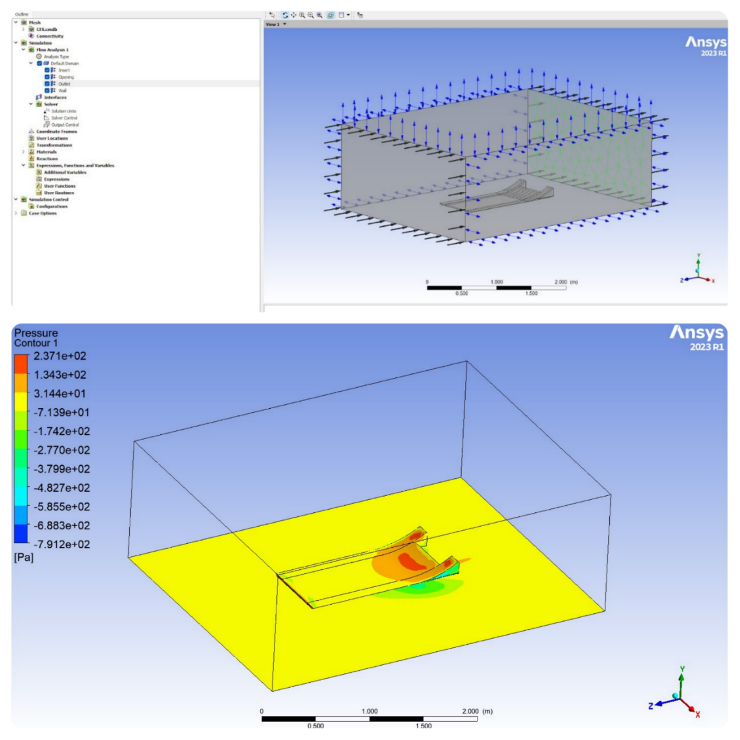
Figure 4: Fluid domain (above) and simulated pressure contour (below) of the diffuser
Our first aerodynamic package
In this section we work with the entire tubular chassis, the nosecone, the diffuser and a prototype of the bodywork to see how much downforce is generated on the wheels and the track.
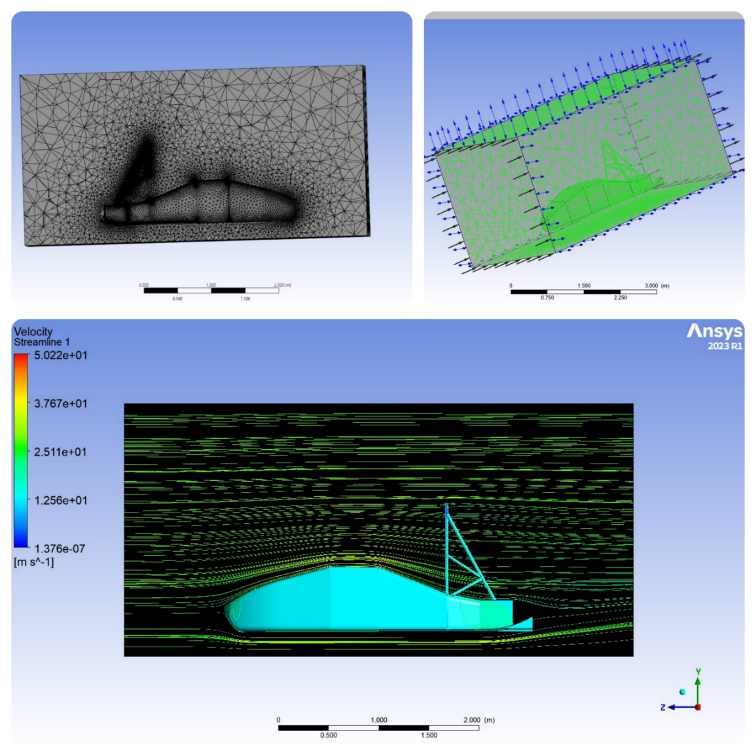
Figure 5: Meshing and fluid domain (above) and simulated velocity streamlines (below) around our early phase of the aerodynamic package
Conclusion
This year of sponsorship have been a difficult year for the aerodynamic team because there were few people, all members had to learn from the beginning how to work with the software, being helped by various professors from the university who understood a little about the program and asking questions in the Ansys community on the internet.
Even with all these difficulties we have been able to carry out the different simulations necessary for our project, as we are now focus in the late part of 2024 season car development.
As a conclusion, we want to thank ESSS and Ansys for trusting us to advertise the software and for having lent us the powerful software for this course, and we hope to collaborate with us the next course 2023-2024. We also know we can do a much better work and extract a lot more from the software, so we are committed to do it.